Protecting drinking water supplies:
Waterproofing municipal water storage tanks
February 01, 2018
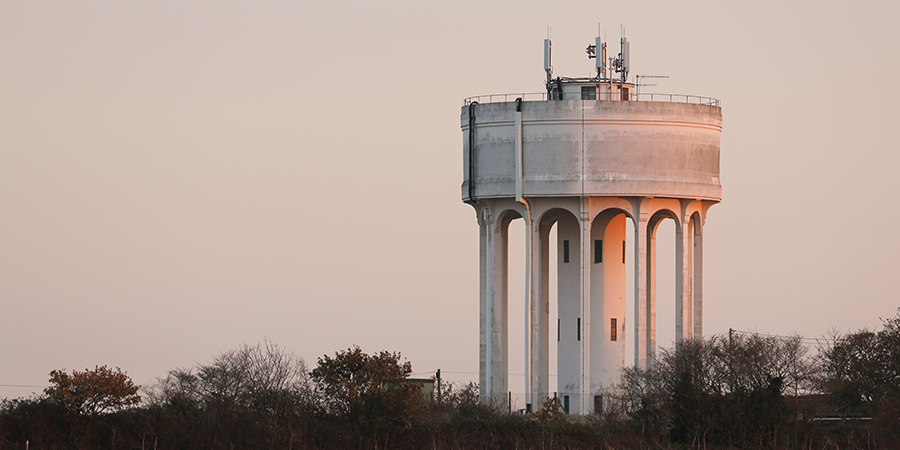
Municipal drinking water tanks are vulnerable to leaks from an array of sources, from ground water infiltration to heat and ice, yet surprisingly many of these tanks are actually not waterproofed. Although the tank itself offers a certain degree of waterproofing protection, over time water can penetrate the structure. Waterproofing a water tank can help keep the community’s drinking water safe and prolong the service life of the structure.
Understanding different types of waterproofing systems
- Integral waterproofing involves adding a special admixture into the concrete mix to make it waterproof. This waterproofing method is relatively inexpensive because there’s no separate waterproofing application required. For this to work, however, it’s important that the quality of the concrete mix and the pouring of the concrete at the job site be maintained. If the ready mix driver adds too much water to the concrete, for example, it can compromise the concrete quality as well as the integrity of the waterproofing.
- Cementitious slurry. This waterproofing method is similar to integral waterproofing except that workers add a layer on top of the concrete substrate instead of adding it into the concrete mix itself. This is simple to apply and is inexpensive. Its application must be carefully controlled to ensure the integrity of the waterproofing membrane.
- Polyurea liquid waterproofing can be used to protect the interior of the water tank. This keeps groundwater or other contaminants from coming into contact with the drinking water inside the tank. Polyurea liquid waterproofing can be used to waterproof pipes and other penetrations as well as tank soffits to prevent decalcification of concrete above the tank water line. For large jobs, it does typically require an investment in spray equipment. However, this seamless liquid alternative is often desirable, due to the speed of application and the durability of the membrane.
- Epoxy liquid waterproofing. This is another option that is easy to apply. However, the elongation of epoxy coatings, at typically 15% compared to polyurea’s typical elongation of 300%, may result in lower flexibility and crack resistance over time. It’s also important to take into consideration the application time, since the curing time is longer than it is with a polyurea membrane.
Key considerations when selecting your waterproofing system
- What will the tank be constructed from? For most steel tanks, pure polyurea liquid waterproofing is ideal. It is also commonly used for concrete tanks. Integral waterproofing has its shortcomings for waterproofing water tanks because it’s part of the concrete itself. Even in the best of circumstances, concrete tends to crack, regardless of concrete mix design and admixtures used. This means that the waterproofing system will have a rather limited service life, unlike polyurea waterproofing, which allows for crack bridging.
Material of the tank |
Waterproofing recommended |
Steel tank |
|
Concrete tank |
|
- Where will the tank be housed? Consider whether the tank will be housed above ground, below ground, or below ground within the water table.
Location of the tank |
Waterproofing applications |
Above ground |
|
Below ground, above the the water table |
|
Below ground, in the water table |
|
- Is there hydrostatic pressure outside the tank? If so, external tanking should be used in addition to an internal polyurea lining to prevent water from absorbing through the concrete, which could harm the polyurea lining and degrade the concrete structure. External tanking can be achieved using waterproofing under the tank slab or on the external face of the walls.
- What government regulations do you need to comply with? To ensure the safety and integrity of the drinking water, it’s critical that your waterproofing system is designed for the application and meets water potability guidelines. Ask your specifying engineer what regulations apply in your area.
- Application time. If the construction time is tight, using a spray-applied waterproofing system is usually best since it can typically be applied two to three times faster than roller applied. Also, consider the curing time. Polyurea liquid waterproofing typically cures in seconds, unlike epoxy, which usually takes weeks to cure.
- Budget. Factor in not just the cost of the system itself but the labour involved, time involved, as well as the service life of the system. For example, the cost of materials and labour for pure polyurea liquid waterproofing is higher than with integral waterproofing and epoxy liquid waterproofing, but the cost over the service life can be significantly lower.
Tags
- Airports
- Architects
- Building Envelope Solutions
- Contractor
- Design Advantage
- Energy efficient solutions
- Subcontractor
- Sustainability
- Waterproofing